Aluminum Casting Illinois: Unrivaled Resilience, Unbeatable Costs
Aluminum Casting Illinois: Unrivaled Resilience, Unbeatable Costs
Blog Article
Understanding the Craft: Specialist Tips for Flawless Aluminum Casting Results
In the realm of aluminum accuracy, casting and competence are paramount to attain remarkable outcomes. Mastering the craft calls for a thorough understanding of the tools and tools at one's disposal, an eager eye for preparing the aluminum alloy to specific specs, and a deft hand in utilizing optimum spreading techniques. However, the true mark of an experienced expert lies in their ability to attain flawlessly smooth surface finishes that raise the top quality of the end product. Quality control and troubleshooting are essential elements that can make or break a casting task, guaranteeing that every step is executed with miraculous care and attention to detail.
Vital Tools and Equipment
Aluminum spreading calls for specific devices and devices to make sure accuracy and effectiveness while doing so. Crucial tools include a crucible, ladle, furnace, and mold. The crucible, generally made from graphite or ceramic products, withstands heats required to melt aluminum. A well-insulated heater with the ability of getting to temperature levels over 1200 ° C is necessary to dissolve the metal. The mold, usually constructed from steel or sand, forms the liquified aluminum right into the desired type. A ladle is utilized to move the fluid steel from the crucible to the mold without spillage.
Furthermore, tools like handwear covers, aprons, and tongs are needed to make certain the safety of operators working with molten light weight aluminum. Spending in high-grade devices and devices not only enhances the precision of light weight aluminum spreading however additionally contributes to a much more reliable and risk-free production process.
Preparing the Light Weight Aluminum Alloy
To guarantee the success of the aluminum spreading process, careful prep work of the alloy is paramount. The very first step in preparing the light weight aluminum alloy is to carefully choose the suitable kind of aluminum based upon the characteristics required for the end product. Variables such as stamina, deterioration resistance, and machinability need to be taken into consideration when selecting the alloy. Once the alloy type is established, it is vital to appropriately clean up the aluminum to eliminate any kind of contaminations that can impact the casting top quality. This can be done with methods like degassing, fluxing, and filtering.
After cleaning, the next crucial step is to heat the aluminum to the appropriate temperature level for spreading. Generally, thorough preparation of the aluminum alloy establishes the structure for an effective casting process and top notch end results.
Ideal Casting Techniques
Executing accurate casting strategies is important for achieving premium results in aluminum casting processes. The light weight aluminum should be heated to the ideal temperature to reduce flaws like shrinking and porosity in the final cast.
Additionally, maintaining regular putting rate and stress is key to attaining harmony in the actors piece. Stable and sluggish putting helps avoid turbulence and air entrapment, which can result in imperfections. An additional important element is the use of degassing agents to remove contaminations and gases from the liquified aluminum, leading to a cleaner end product.
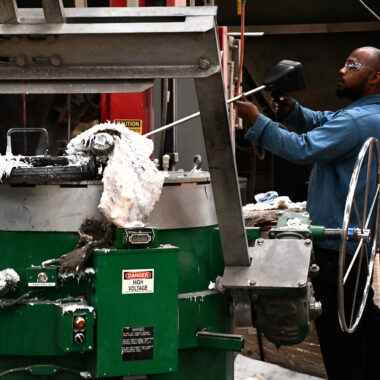
Achieving Smooth Surface Area Finishes
For suppliers seeking to boost the visual allure and top quality of their aluminum spreadings, accomplishing smooth surface area finishes is an indispensable element complying with accurate casting strategies and proper air conditioning treatments. One key method to achieve smooth surface coatings is by utilizing high-grade molds that are correctly prepared and preserved. The mold and mildew surface must be carefully cleaned up and covered with release representatives to stop flaws transferring onto the actors light weight aluminum during the cooling process.
Additionally, regulating the cooling price of the light weight aluminum spreading is critical for achieving a smooth surface finish. Rapid cooling can lead to thermal gradients that cause surface flaws, while sluggish air conditioning might trigger microstructural concerns - aluminum casting illinois. By carrying out regulated cooling processes, such as making use of air or water quenching approaches, manufacturers can make sure that the aluminum strengthens consistently, reducing the chance of surface area imperfections
Along with mold top quality and cooling down treatments, post-casting treatments like shot blasting or chemical etching can further fine-tune the surface area finish of aluminum castings. These strategies help smooth out any remaining roughness or pollutants, resulting in a remarkable look that meets the finest quality standards.
Quality Assurance and Troubleshooting
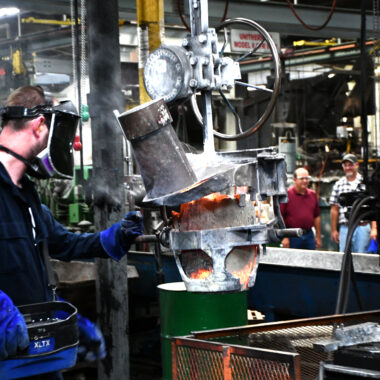
In the realm of troubleshooting, it is important to have a thorough understanding of typical flaws that can occur throughout light weight aluminum spreading, such as shrinking, surface area, or porosity irregularities. By performing origin cause analysis and applying restorative procedures, producers can protect against these defects from persisting in future spreading runs. Reliable repairing not only boosts the total high quality of actors aluminum items however additionally boosts process effectiveness and reduces manufacturing prices. Constant enhancement with top quality control and repairing methods is fundamental to achieving flawless lead to aluminum spreading.
Verdict
Finally, grasping the craft of light weight aluminum casting calls for crucial tools and tools, proper prep work of the aluminum alloy, optimal casting strategies, achieving smooth surface finishes, and executing quality assurance measures. By complying with these expert pointers, flawless results can be accomplished in light weight aluminum spreading procedures. Quality assurance and troubleshooting are crucial aspects my website to take into consideration to make sure high-quality and consistent lead to light weight aluminum spreading jobs.
The initial action in preparing the aluminum alloy is to carefully choose the ideal type of aluminum based on the attributes required for the final product.Implementing specific spreading strategies is important for attaining top notch results in aluminum casting processes. By grasping these optimum casting methods, suppliers can consistently produce perfect light weight aluminum spreadings.
For suppliers looking for to boost the aesthetic charm and quality of their light weight aluminum spreadings, attaining smooth surface area coatings is an important element complying with exact spreading methods and appropriate air conditioning treatments.In final thought, grasping the craft of aluminum casting requires vital tools and devices, appropriate preparation of the Read Full Report aluminum alloy, optimal spreading strategies, attaining smooth surface area coatings, and implementing quality control steps.
Report this page